- Small, lightweight, stretchable, cost-efficient thermoelectric devices signify a breakthrough in sustainable energy development and waste heat recovery.
- Next-gen flexible energy harvesting systems will owe their efficiency to the integration of graphene nanotubes. They offer easy processability, stable thermoelectric performance, flexibility, and robust mechanical properties.
- Nanocomposites have high market potential in manufacturing generators for medical and smart wearables, vehicles sensors, and efficient building management.
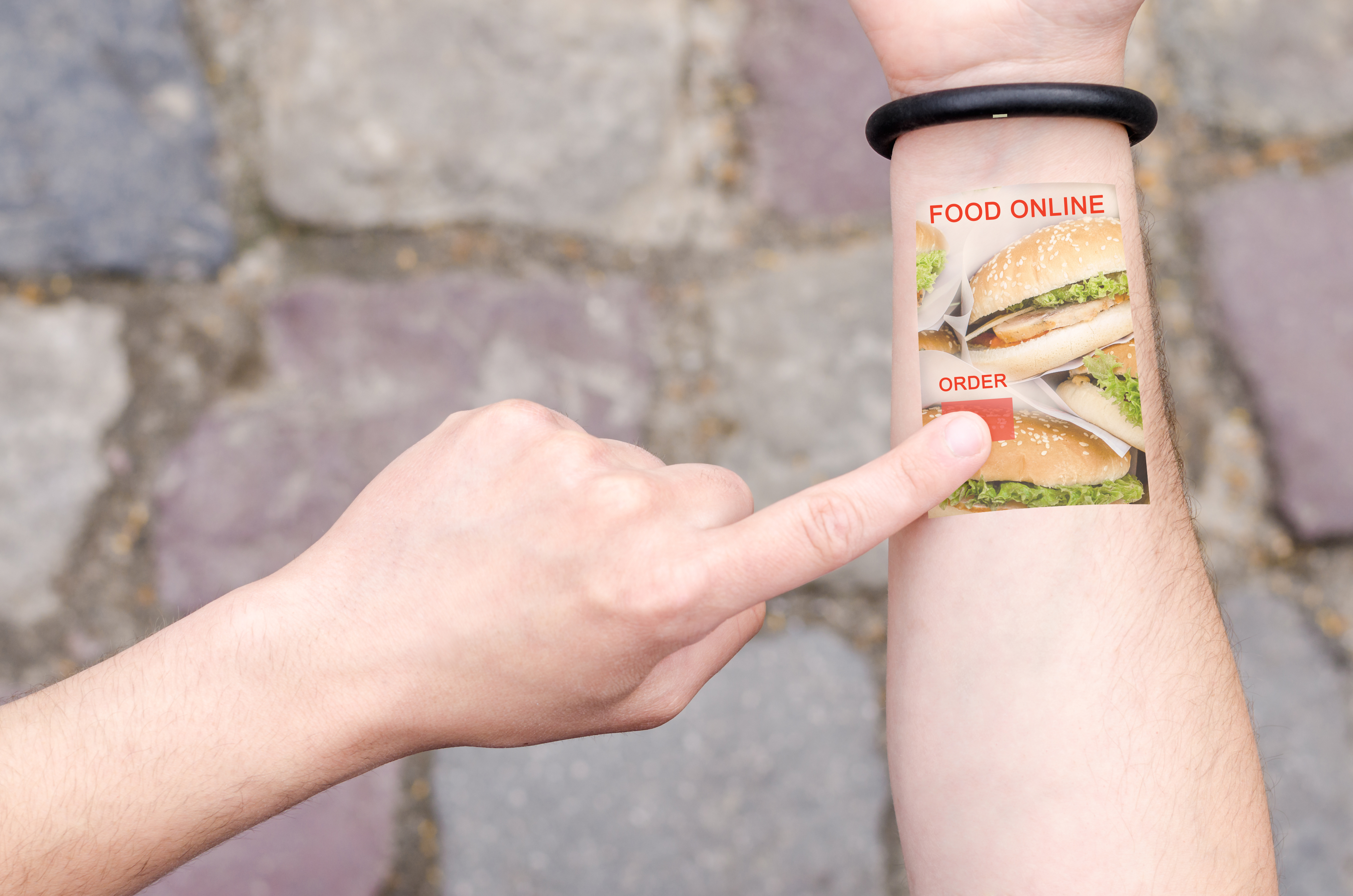
Around half of the world’s useful energy is wasted as heat due to the limited efficiency of energy conversion devices. For example, one-third of a vehicle’s energy dissipates as waste heat in exhaust gases. At the same time, vehicles contain more and more electronic devices requiring electrical energy. As another example, lightweight wearable sensors for health and environmental monitoring are also becoming increasingly demanding. The potential to convert waste heat or solar energy into useful electrical power has emerged as an opportunity for more sustainable energy management. Convenient thermoelectric generators (TEGs) currently have only low effectiveness and a relatively large size and weight. Based on expensive or corrosion-vulnerable materials, they are rigid and often contain toxic elements.
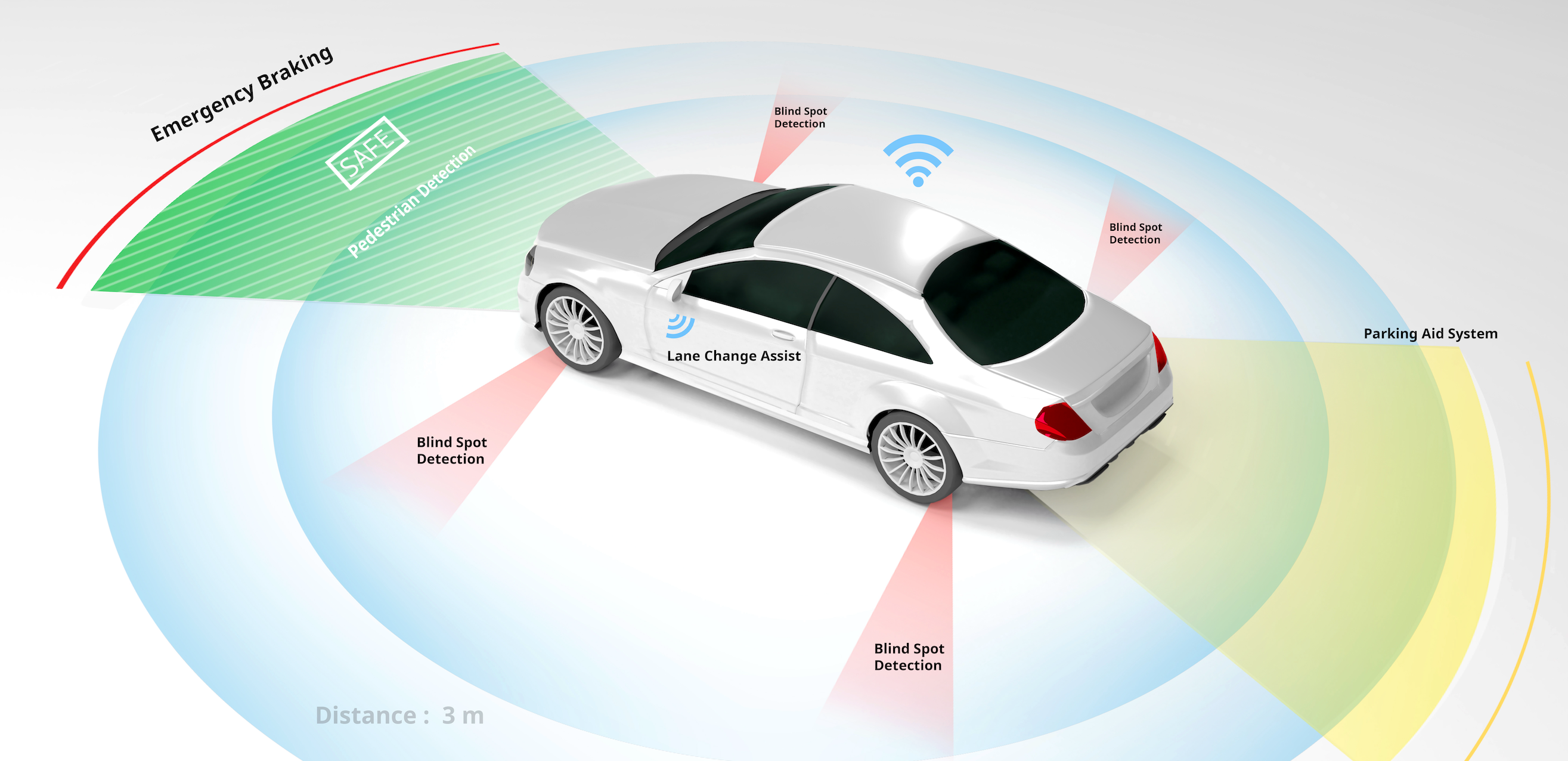
Recently developed, easy-to-process, self-supporting and flexible nonwoven nanocomposite sheets demonstrate excellent thermoelectric properties combined with good mechanical robustness. A recent paper in ACS Applied Nano Materials described how researches combined a thermoplastic polyurethane (TPU) with TUBALLTM graphene nanotubes to fabricate a nanocomposite material capable of harvesting electrical energy from sources of waste heat.
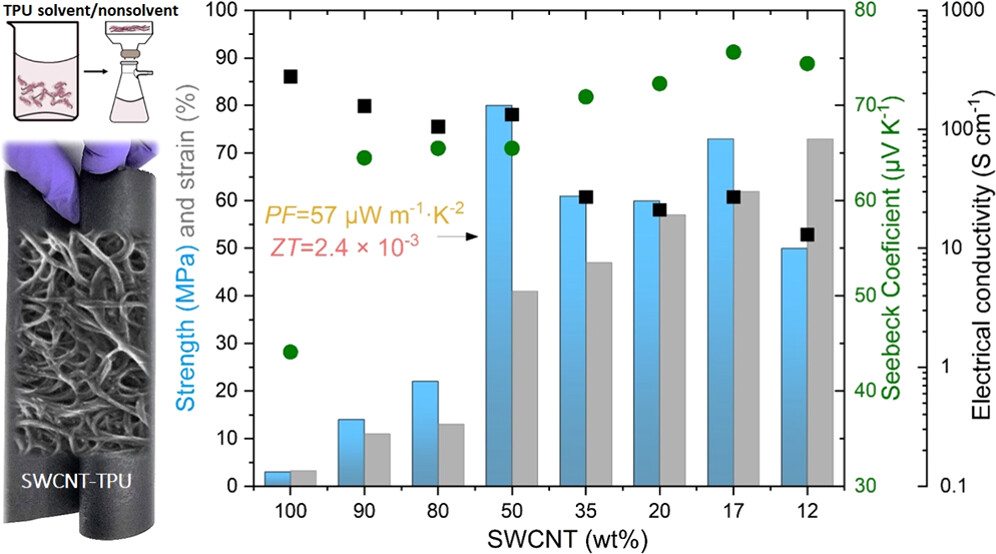
Thanks to their high aspect ratio and specific surface area, graphene nanotubes provide TPU with electrical conductivity, making it possible to achieve high thermoelectrical performance while maintaining or improving mechanical properties. “Stiffness, strength, and tensile toughness were improved by 7, 25, and 250 times compared to buckypapers, respectively. Nanocomposite sheet shows low electrical resistivity of 7.5*10-3 Ohm×cm, high Young’s modulus of 1.8 GPa, failure strength of 80 MPa, and elongation at break of 41%,” said Dr. Beate Krause, Group Leader, Leibniz-Institut für Polymerforschung Dresden e. V.
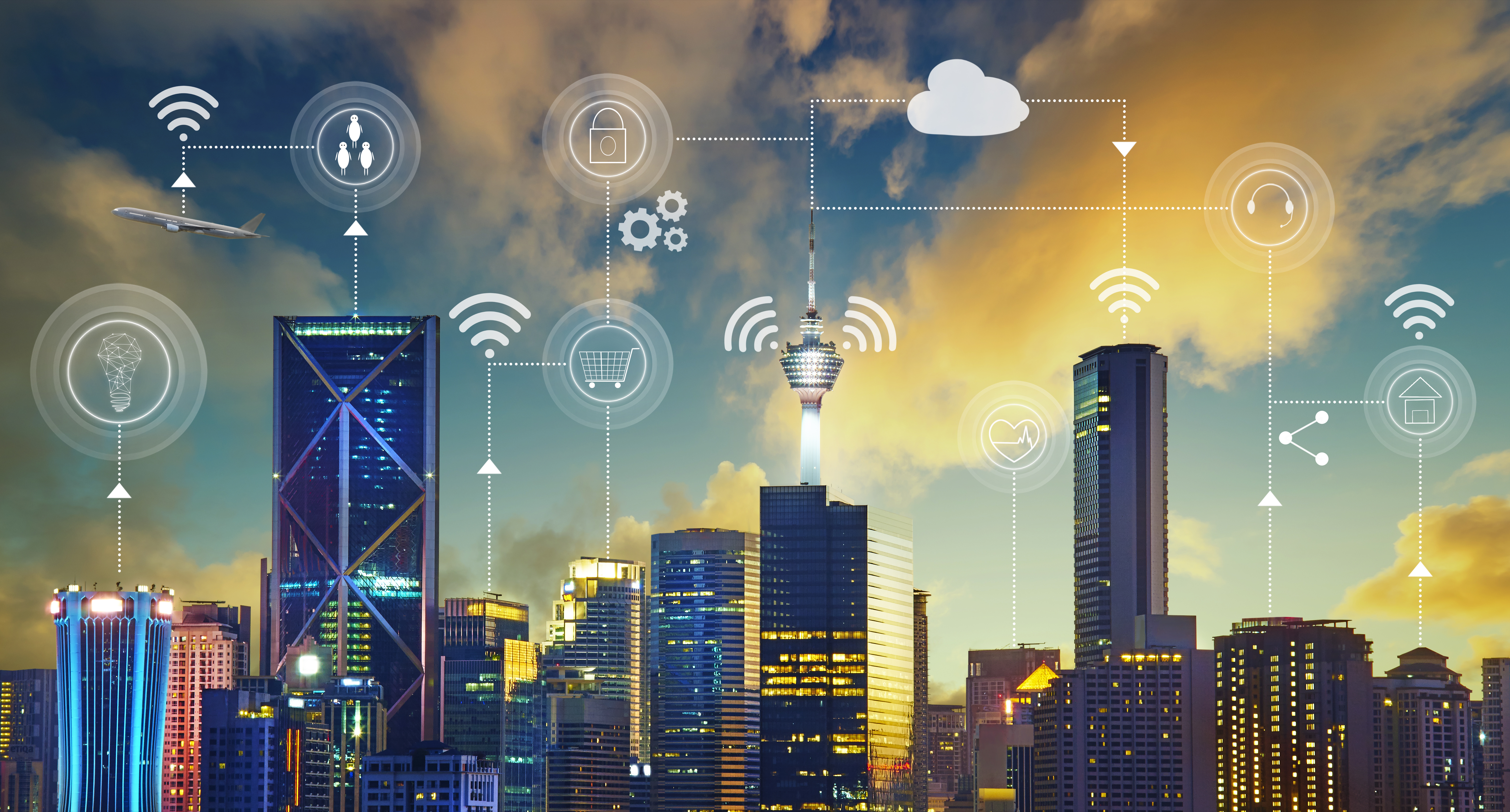
Graphene nanotubes, being a fundamentally new material, provide an opportunity to replace current TEG materials with more environmentally friendly ones. The sensors powered by such thermoelectric generators could act as a “smart skin” for vehicles and buildings, providing sensoring capabilities to monitor performance and prevent potential issues before they lead to breakdowns, ensuring optimal operational efficiency. In aircraft, no-wire nanocomposites could serve as stand-alone sensors for monitoring deicing systems, eliminating the need for an extensive network of electrical cables. The high flexibility, strength, and reliability of graphene nanotube-enabled thermoelectric materials also extend their applications into the realm of smart wearable and medical devices.
---
Leibniz-Institut für Polymerforschung Dresden e. V. is one of the largest polymer research institutions. As a member of the Leibniz Association, the institute conducts fundamental application-oriented research. Strategic topics include fundamental concepts of soft matter, bioinspired materials, functional materials and systems, process-controlled structural materials, data science-based material research, sustainability, and environment protection.
Website: ipfdd.de
Headquartered in Luxembourg, OCSiAl is the world’s leading manufacturer of graphene nanotubes, also known as single wall carbon nanotubes. OCSiAl produces high-purity graphene nanotubes under the brand name TUBALL™ and accelerates the transformation process of nanotubes from the laboratory to being an industrial-scale material by simplifying their handling. The company’s sales force and distributor network cover more than 50 countries worldwide.
Website: tuball.com